BY ANDREW BAILEY
BG Independent News Correspondent
Sustainability in the agriculture industrial sphere is an achievable, energy efficient, and cost-saving “process engineered solution” for large businesses and small farmers alike, according to Doug Medley, technical project manager for Matrix Technologies.
The Center for Innovative Food Technology presented “Sustainability in Agriculture” for its May Agribusiness Forum series, which provides education on current issues and trends affecting agriculture.
Medley, a professional engineer and certified energy manager, some about the importance of sustainability in the agro-industrial environment, and what it looks like in practical application.
He started by defining and “demystifying” sustainability, which he said can be mistaken for an expensive and overbearing investment.
The idea of sustainability is not a recent development, Medley said, defining it as renewing resources at a rate equal to or greater than the rate at which they are consumed.
“It meets the needs of the present but doesn’t compromise on meeting needs in the future,” he said.
The concept was born when the National Environmental Policy Act was passed in 1969, to ensure environmental consideration from U.S. industries. A year later, the Environmental Protection Agency was formed, the Clean Air Act was passed, and the Clean Water Act followed in 1972.
These acts, and the EPA’s formation, began the discussion on sustainability. But 50 years later, Medley said misconceptions that “it’s just a bunch of regulations” and “it’s getting in the way of running a business” still exist.
He said if implemented properly, sustainability programs shouldn’t do this.
“Operating in a sustainable way is the same as operating in an efficient way,” Medley said. “Companies that pay attention to their sustainability typically function better in the long run.”
Sustainability efforts lead to cost-efficiency, increased stakeholder equity, and environmental stewardship, and if kept up and publicized over a period of time, an improved corporate image as well.
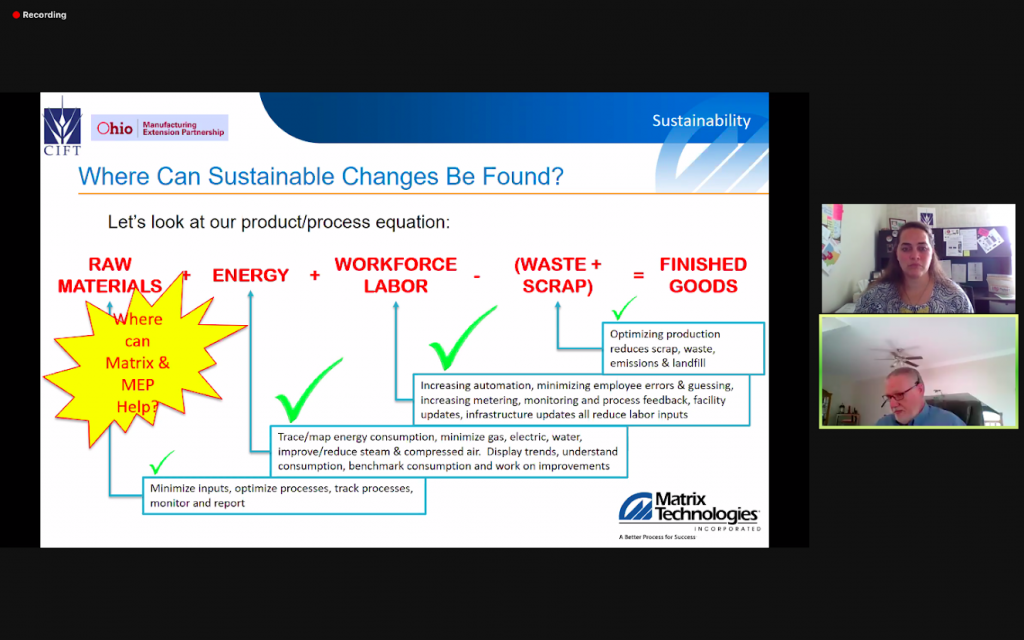
Medley explained the manufacturing process of sustainability in a simple equation: Raw materials + Energy + Workforce labor – Waste and scrap = Finished goods.
He said the goal of any sustainability program is to minimize the inputs on the left side of the equation to maximize production of goods.
It’s a simple model, but it clearly shows the reason for sustainability, because it serves the business’ cost-saving needs and the more universal goals of environmentalism.
Matrix Technologies, headquartered in Maumee, is a company with decades of experience in automation and engineering projects in over 40 countries and has serviced a variety of companies in Northwest Ohio and the surrounding region, such as Campbell Soup, Mondelēz International, ADM Grain, and Jim Beam.
But implementing sustainability programs in agro-industrial plants can be difficult due to the hundreds of variables in motion for them to function on a daily basis.
Medley clarified that sustainability is a continuous process, not a single action. The first step in this process is for a facility to monitor its sustainability, which is more than just glancing at gas, electric, and water bills when they come in.
Medley circled back to the instrumental equation, saying that Matrix and the Ohio Manufacturing Extension Partnership, of which CIFT is an affiliate, assist in minimizing the left side of the equation.
To find opportunities for sustainable change, they begin by highlighting areas in a facility’s processes that may be cost-inefficient, harmful to the environment, or underproductive.
In industrial plants specifically, he said, companies should closely examine utilities, using the acronym WAGES — water, air, gas, electricity, steam — to optimize energy consumption.
Then comes the creation of energy use indexes and benchmark goals to meet, from individual processes to whole departments.
“Energy should be viewed as an ingredient to make things easier,” he said, and measured as a raw material.
Some energy saving areas are low-hanging fruit, he said.
If a machine doesn’t sound right, it probably needs to be fixed, and until it is fixed, it should be considered an energy loss.
This is why all employees need to be familiar with the concept of sustainability and how it can be practically applied in a facility, Medley said.
Thinking about everything as a “process” can help expedite sustainability efforts. This means having Medley’s foundational equation in mind when examining energy consumption.
Publicizing successes and failures can help bring goodwill to a company’s reputation too, he said.
Accounting for every process a company undergoes, from daily manufacturing to less regular processes is key to sustainability.
“If you can’t see it, you can’t control it,” one of Medley’s slides said.
Understanding every complex system in a facility can be a challenge, but by collaborating with Matrix and MEP, professional engineers like Medley can help find the best solutions, he said.
In a Q&A session after the presentation, Medley noted some solutions to automate processes that he assisted in, many of which are simple fixes if done the correct way.
He said a local bourbon company switched from fire-burning boilers to electric boilers, increasing their efficiency to 98 to 99 percent.
Sometimes, the symptom is just that, a symptom. It’s not always a problem.
A company he assisted was having an issue with its freezer compressor and requested assistance in replacing. But upon inspection, Medley found that it was the freezer itself that was the problem.
“It was leaking a ton. Closer inspection and pragmatic solutions can be really beneficial in these kinds of situations,” he said.
So, they switched the freezer for a more cost-effective and environmentally friendly one and the issue was resolved.
Medley said sustainability is something every company large and small should strive for, it’s just a matter of education on the benefits of it.
“At its core, it’s about making every operation as efficient as it can be,” he said.
This means a “data driven, transparent and pragmatic” strategy.
If done correctly, it helps the environment, as well as saves resources, like money.
CIFT’s next Agribusiness Forum is on June 17 from 8:30 to 9:30 a.m., titled “Introduction to the Airable Research Lab at Ohio Wesleyan University,” with speaker Barry McGraw, founder and CLO of Airable Research Lab.
Elizabeth Murawski, business and workforce development manager for CIFT, said in-person components for the Agribusiness Forum are in consideration for August, dependent on health and safety guidelines regarding the coronavirus.