By JAN LARSON McLAUGHLIN
BG Independent News
Turns out it’s pretty expensive to take the stink out of sewage.
After hearing complaints for years about the unappetizing odors from the city’s wastewater treatment plant on Dunbridge Road, east of Interstate 75, Bowling Green officials have been installing a series of updates to the facility.
Last week, the city’s board of public utilities took a step toward the next update – this one costing $525,000. City Council will hear the first reading on this expense Monday evening.
This comes after the installation of two activated carbon filters at the septage receiving station to address odors from the truck unloading bay. And after the installation of two activated carbon air filters at the biofilter, along with a larger suction fan that allows for increased air flow. And installation of an activated carbon air filter on the grit and headworks building.
“While these projects have made considerable improvements to odor issues, there is still more work to be done,” said Bowling Green Public Utilities Director Brian O’Connell.
The next step, approved Monday evening by the board, calls for replacement of the aluminum biofilter tank covers, cleaning of the inside tank walls and use of an anti-corrosive additive.
O’Connell explained that the new concrete covers should be more durable and allow for the proper environment to treat the biosolids.
Currently, the larger suction fan used in the tanks pulls the air off the top of the covered tanks to send it to the biofilter and carbon filter. But because the aluminum tank covers are worn, the air seals that are supposed to keep the odors inside the tanks can leak – allowing the odors to escape untreated.
“Once the new covers are on, it should seal off any odors from the tanks themselves,” O’Connell said.
The current tank covers also don’t allow for the large suction fan to be used at its peak strength. The fan has to be throttled back out of concern that the tank covers may collapse due to the strong suction, O’Connell explained.
The concrete tank covers are expected to last longer than the aluminum, since they won’t corrode, should hold a better seal, and will have hatches to allow access to the interior.
“I think long-term this will be a better fit,” O’Connell said. “It does work under harsh conditions.”
Once the solids from sewage treated at the plant goes through the biosolids process, it is rated as a Class A biosolid, meaning it can be blended with topsoil and applied to land.
Even when the tank covers are replaced, the work to stop odors at the plant will not be completed, O’Connell said.
The next step will involve getting rid of giant blowers at the site, and installation of smaller, more efficient and more targeted blowers. That project will cost an estimated $4 million to $5 million.
City Council will make the final decision on the tank cover project.
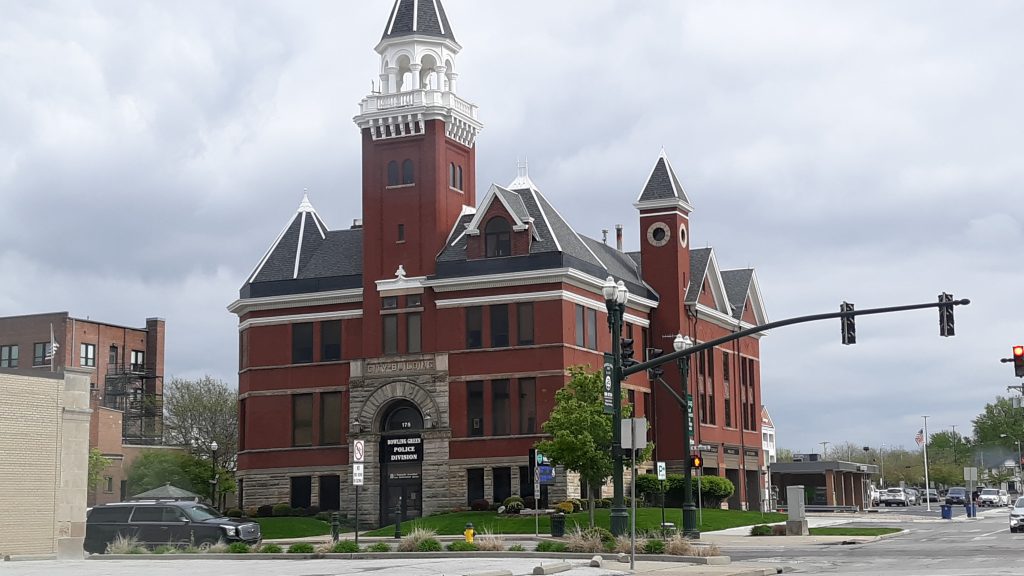
Also at last week’s meeting, the public utilities board agreed to use electric funds to help upgrade the HVAC system in the Police Division building at the southeast corner of West Wooster and South Church streets.
Several city buildings were evaluated for potential energy efficiency projects, capital costs and possible annual savings. The evaluation found the police building to have the greatest need for an HVAC and lighting upgrade. It was determined the building is a high user of energy per square foot.
It was estimated the improvements would cost $575,000, and the savings would be about $27,000 a year.
Because the electric service to the police building is paid for from the city’s electric funds, the improvements would result in a savings, O’Connell said.